E-Panel™
產品查詢In the process of flat-panel-display manufacturing, a production panel (array or color filter) passes through many process steps where electrostatic charges can be generated particular on the glass backside surface due to friction. These electric fields are going through the dielectric glass panel and induce potential differences in the front-side pattern and can result in ESD damages. Even in manufacturing processes with well engineered electrostatic protection concepts, there are always areas in which electric fields can affect the panels or where charges can remain for long time on isolated surfaces. Particular conveyor rollers charge the backside glass surface and increased particle deposition on the front and backside.
The measurement of electric fields or electrostatic charges in the highly automated manufacturing of flat-panel-displays is tricky. It is difficult to obtain realistic and reliable data regarding the endangering electrostatic potentials and local field strengths at all locations in the production environment.
Even when one succeeds by using a suitable measuring device to measure the ambient field intensity at all locations through which the glass sustrates normally passes, from the goods receiving area through visual inspection stations, handling robots, stockers, transportation systems etc., it cannot be guaranteed that the measured values will apply under normal manufacturing conditions, particularly when the glass itself is present.
The situation inside the production tools is even more critical. Numerous friction processes happen during the FPD manufacturing, potentially creating critical electrostatic charges on the glass substrates. Clamping and unclamping on vacuum chucks or electrostatic chucks, friction between liquids and glass surfaces in cleaning processes, and interactions between gases and the substrate surface are well known risk factors. These charges can create ESD events, non-uniform surface conditions or result in increased particle deposition.
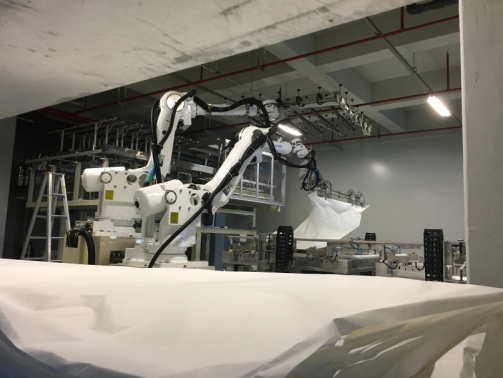
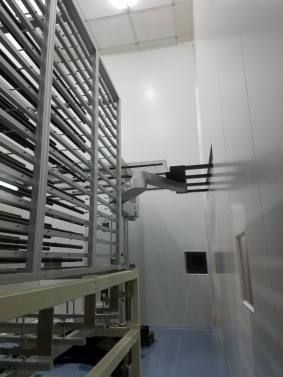
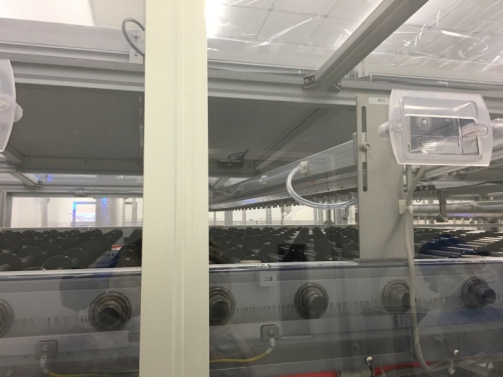
Therefore, continuous control over hazardous electrostatic potentials for the substrates in FPD production is an absolute necessity quality assurance measure.
E-PANELTM is made from a 100 mm by 1000 mm or 700 mm polyimid flexible board which will be applied to a bare glass panel on site at the user via a permanent high efficient adhesive film. Eight sensing areas are distribute linear with equal distances over the 1000 mm or 700 mm length. A controller-box contains the electronics and battery and contact-points for a computer interface. The entire measuring system is hermetically closed covered all around with a highly chemical resistant polyimid layer. The maximum thickness of E-PANELTM is 1.05 mm.
Within E-PANELTM there are 8 electrostatic voltmeters which measure the electric potential difference between 8 sensing areas and a „virtual ground“ in the controller box. These values can be converted to critical field-strengths. A real-time clock in the device assigns the clock time to the measured values. The measured values along with the clock times assigned to them are recorded in a memory with a sampling rate of 10 Hz.
Battery charging, communication, data-transfer, neutralizing and zeroing is done via special switchable contacts by a manual handled interface which can be easily connected to the control-box and is fixed by magnetic forces. The interface is connected to a computer USB port.
E-PANELTM operating software enables the measurement and can download the measuring data.
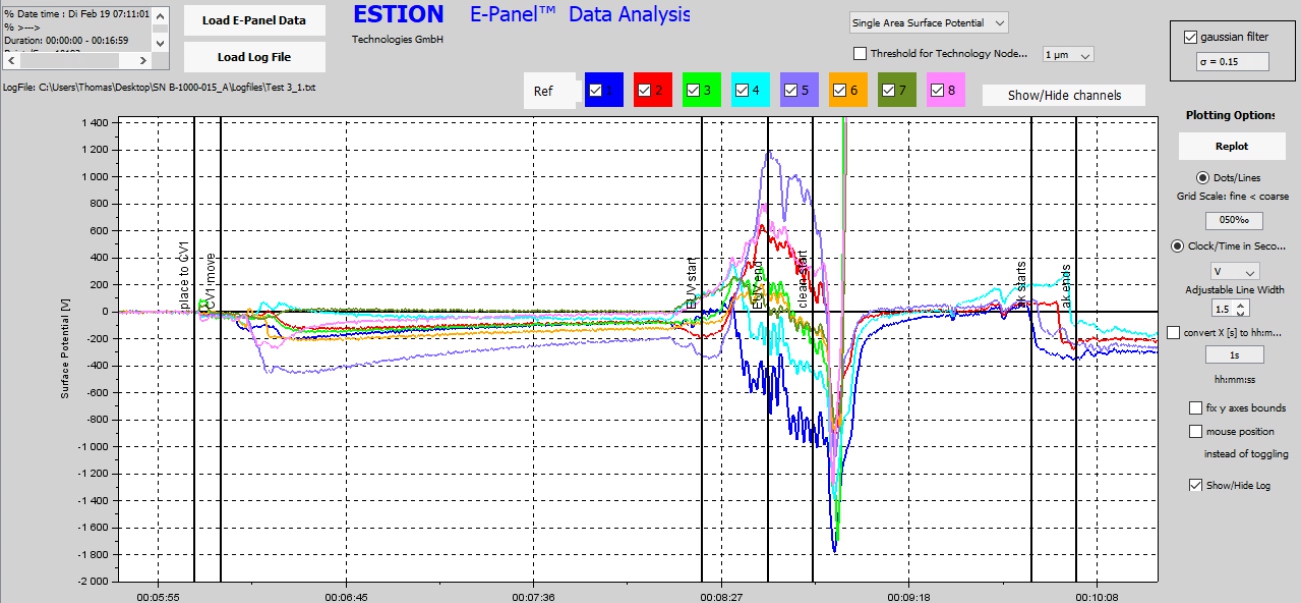
The measurement starts at any location in the production line before the process of interest. Then the E-PANELTM can be exposed for up to about 2 hours of battery operating time to the manufacturing processes. The system is hermetically sealed and can be immersed in wet processes and also handled in vacuum.
The measurement data from E-PANELTM can be transferred to a PC where they can be evaluated with a specific analysis software. Process log files can be synchronized.
Specifications: