Simco-Ion’s Model 5635M AeroBar MP ionizing bar is specifically designed to eliminate static charge in semiconductor and other ultra-clean manufacturing processes where fast discharge time, low swing voltages and precision balance are required, but exposed metallic surfaces are not permitted. The Model 5635M utilizes MP technology, combining a high frequency sine wave with modulated pulses (MP) for high ion output and delivery. This breakthrough technology enables AeroBar mounting within 150 mm of the wafer. MP technology, combined with ultra-clean silicon emitter points and precision adjustment, provides ISO 14644-12 ionization (0.01 mm particles or nanoparticles) and ISO 14644 Class 1 (0.1 mm particles) cleanliness, critical for smaller technology nodes. For processes that do not require extreme cleanliness, the optional air-assist accelerates ion delivery, providing faster discharge times and performance over longer distances. MP technology is easy to adjust and features the ability to fine-tune voltage, frequency and balance to meet differing environmental and product sensitivity requirements. Shorter bars (<600 mm) feature 50 mm spacing between nozzles, to improve ion distribution in close applications.
Features:
- ISO 14644-12 (0.01 µm particles) cleanliness
- Modulated pulse technology
- Metal-free design "M"
- Excellent lateral uniformity
- Low field voltages
- Air-assist capability
- Optional software with easy-to-use interface
- Alarm output signal
Benefits:
- Compatible with all wafer technology nodes including 14 nm and below
- Precision balance, high ion output, long-term stability
- Perfect for "No Metal" applications
- Uniform balance across the AeroBar
- Safe placement as close as 150 mm of the wafer or reticle
- Enhanced static charge neutralization at fast automation speeds
- Fast setup and easy optimization in any environment
- Communicate to tool or facility monitoring system
Specifications:
5635M |
|
Input Voltage | 24 VDC ± 10% |
Output Voltage | 13.5 kV p-p (max), adjustable |
Distance | 150 - 1000 mm distance to surface; application & customer specification dependent |
Frequency | Default setting at 5 Hz; adjustable from 1-33 Hz |
Balance | Auto balancing system <±20V over time and across the bar length (measured in a controlled environment at 24" distance) |
Ion Emission | Modulated pulse (MP) technology |
Emitter Points | Single crystal silicon emitter points |
Emitter Pitch | 50 mm spacing between nozzles on 350-600 mm length bars; 75 mm spacing on longer bars |
Ionization Performance |
15 sec (typ) with no air-assist, Vp-p Swing of 80 Vp-p; measured at 24” below an emitter center group of points |
Cleanliness | Meets ISO 14644-12 cleanliness (0.01 µm particles or nanoparticles) and ISO 14644 Class 1 (0.1 µm particles) using 45-50% output voltage setting |
Air Supply | Clean dry air (CDA) or nitrogen |
Airflow | 45 psi max gas pressure; 1-3.5 lpm/nozzle thru 8 mm OD one-touch fitting (optional) |
Ozone | < 0.05 ppm |
EMI | Below background level |
Operating Env. | Temperature 15-35ºC (59-95ºF); humidity 30-60% RH, non-condensing |
Bar Settings | DIP switches for general power settings; trimpots for fine tuning balance, frequency, and power output or use the serial output to the MP 5635 Bar Control software for fine adjustments |
Enclosure | ABS chasis (ground plate - carbon filled ABS) |
Dimensions | 3.1H x 1.3W x 14/18/24/34/39/45/51/57/63/69/75/81/87/93L in. (78H x 34W x 350/450/600/ 850/1000/1150/1300/1450/1600/1750/1900/2050/2200/2350L mm) |
Certifications | ![]() |
Model 5601 Power Distribution Box |
|
Input Voltage | 24 VDC for each bank of 4 bars; 5.6A total (0.7A max/port) |
Communication | Ethernet (RJ-45) to/from PC; individual bar standby inputs |
Alarm Output | Relay closure to ground |
Output | 8 RJ-45 ports (1 for each 5635 bar) |
LED Indicators | Green PWR, Yellow COM, Red ALM, Blue USB |
Weight | 15 oz (420g) |
Dimensions | 1.2 H x 6.3L x 3.6W in (3.1H x 16.0L x 9.2W cm) |
Certifications | ![]() |
Simple Installation
The Model 5635M ionizing bar is quickly installed by simply plugging into a 24 VDC source and connecting an air line, (if air-assist is desired). Set the DIP switches for general power levels as defined in the user’s manual to activate factory settings for a base discharge performance. Users can then fine-tune the control parameters from the bar or through the easy to use software GUI for installations where optimized balance, swing voltage and discharge times are desired. An alarm connection in the Signal and Power Junction Box enables a signal output to the tool or central computer for FMS monitoring.
Cleanliness
Model 5635M is designed to operate in and maintain ISO 14644-1 Class 1 cleanliness (10 particles or less per m3 for particles of 0.1 micron and larger). Model 5635M will also perform to ISO 14644-12 cleanliness (1200 particles or less per m3 (34 particles per ft3) for particles of 0.01 micron and larger) when operated at 45-50% output voltage setting and OpenJet nozzles with single crystal silicon emitters.
ISO 14644-1 (1999) establishes 9 particulate class limits. A class is met when airborne particles-per-cubic-meter (or particles-per-cubic-foot) do not exceed the class limit. The following graph summarizes the class limit lines for particles between 0.1 micron and 5 microns.
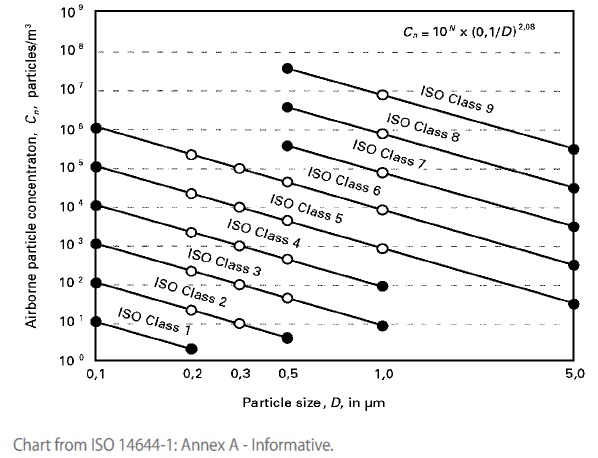
The Model 5601 Power Distribution Box can be used to centralize power and software control for up to 8 MP AeroBars.
Ordering Information
91-5635U-xxxx- yy-zzzzz |
xxxx (bar lengths): 350*/450*/600*/850/1000/1150/1300/1450/1600/1750/1900/ 2050/2200/2350 mm; yy (nozzle spacing): -50 for 50 mm, -75 for 75 mm; zzzzz (nozzle type): OpenJet |
33-5601-03 | Power Distribution Box |
14-21241 | Power Supply (Power Distribution Box only) (an appropriate power cord is required) |
33-21491 | Signal and Power Junction Box for FMS |
92-5635-001 | AeroBar MP Remote Serial Adapter Kit (includes RJ-45 splitter, serial to USB adapter, RJ-45 to DB9 |
33-25625 | 24 VDC Power Converter Box with Signal and Power Junction Box Kit |
25-0540-xx | CAT5 with RJ-45 Ethernet Cable in 6', 10', 15' lengths, white |
32-22210 | Flat Mounting Bracket (delrin); recommended usage: 350-1000 mm 2 brackets, 1350-1650 mm 3 brackets, 1800+mm 4 brackets |
32-2214-01 | Bracket Swivel (Delrin) |
33-2215-01 | Bracket Assembly (Delrin) includes 32-2212-01 & 32-2214-01 |
*The 350, 450 and 600mm are only available with 50 mm nozzle spacing.